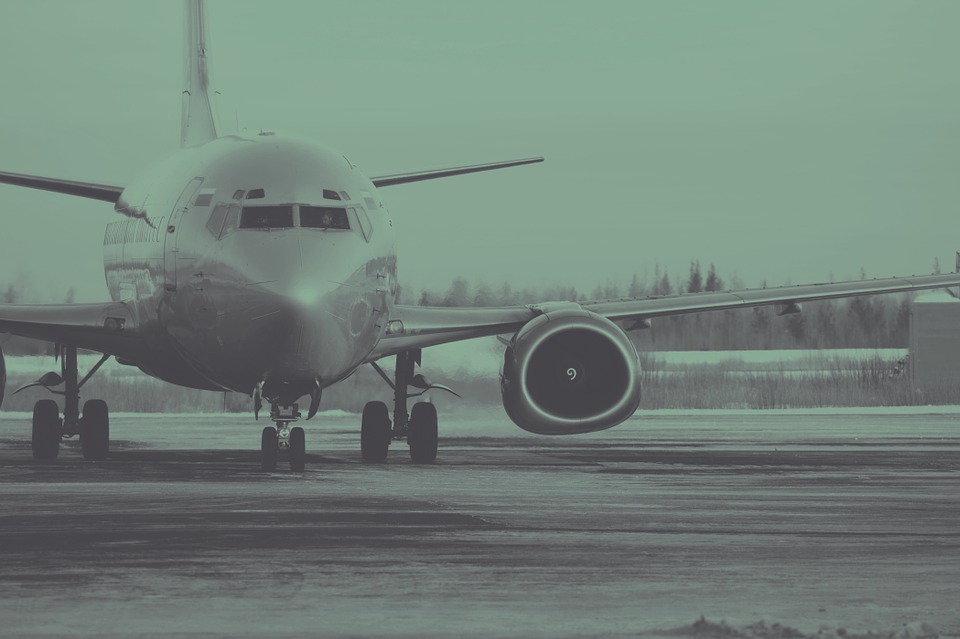
ISO 9001, managed by the International Organisation for Standardisation (ISO), is an international standard that organisations and businesses follow when implementing a QMS (quality management system). As such, it is able to be utilised by any service or manufacturing company in any industry sector. AS9100, however, is designed for exclusive use by defence, aviation and space organisations, often known as the aerospace industry and is managed by the International Aerospace Quality Group (IACG) and the Aerospace Department of SAE International. So, what does the AS9100 standard consist of that makes it different from ISO 9001? Let's find out!
AS9100 Structure
The structure of the AS9100 standard has been built on the foundations created by the ISO 9001 standard, as this has become the fundamental requirement for implementing a QMS for many organisations around the globe. The AS9100 standard takes the same requirements found in ISO 9001 and simply adds additional notes throughout. As a result, it would be feasible to implement a QMS that is compliant with ISO 9001, with the implementation of these additional requirements that apply only to a smaller division of your company that engages with the aerospace industry.
AS9100 Additional Requirements
One of the major additions that the AS9100 standard focuses on is in the requirements for 'planning for product realisation', which includes a greater emphasis on risk and product management, control of work transfers, and configuration management of products. Risk identification and assessment are seen as essential components within the aerospace community, therefore these are carried throughout each requirement of the standard.
Another addition occurs in the 'design and development' section of the standard. Additional prescriptive requirements for testing and documentation are included as well as instructions for design validation and verification. This section of design changes is linked back to the added section on configuration management.
The largest amount of change occurs in the 'product and service provision' section of the standard, which sees the biggest difference in implementation from industry to industry. A number of important requirements involve control of changes to production processes, support after delivery and specific product preservation methods such as shelf life control, which are common within the aerospace industry.
Application of AS9100
These are just a number of the many additional requirements that AS9100 adds to the IS0 9001 standard for the specific use within the aerospace industry. As a result, these added requirements have little application outside of the industry. If you have parts of your company that are related to this industry or are thinking about adding departments which focus on the aerospace industry, taking the time to look into the possibility of adding the specialised requirements may be of some benefit and a good first step.
If you require any assistance with a quality management system or with achieving ISO 9001 certification, please do not hesitate to contact NPT Management Systems today.
Contact Us >
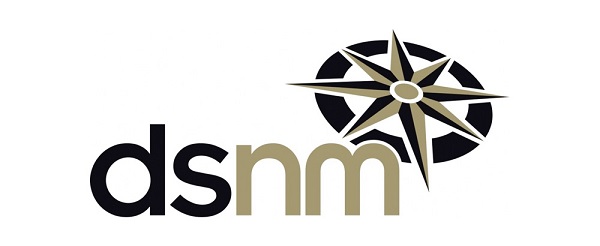
DSNM Ltd, established in 2000, is a company that works within the superyacht industry, providing a range of both products and services to its expansive client base. Formed on the need for bespoke yacht packages, DSNM works alongside the Designated Person Ashore from a variety of yacht management companies and many private clients.
DSNM state that their ethos is built on constantly improving their service and offerings to their clients, being proactive and developing relationships that enable them to become a first choice service provider in the navigational field. With a team boasting a combined experience of 50+ years, DSNM has become a market leader within its field, so it came as no surprise when they approached us to assist with their ISO 9001 accreditation.
Some time has passed since DSNM achieved ISO 9001 status, therefore, it was time for a surveillance audit to ensure that the practices and procedures that we helped put into place with a quality management system were still being adhered to. It's with great pleasure to announce that, with our on-going assistance, DSNM has passed their ISO 9001 audit with zero non-conformities - brilliant news!
This is another milestone in our fantastic working relationship with DSNM who can now continue on their journey in the superyacht industry to maintain their position as market leaders.
If you require any assistance with a quality management system or with achieving ISO 9001 certification, please do not hesitate to contact NPT Management Systems today.
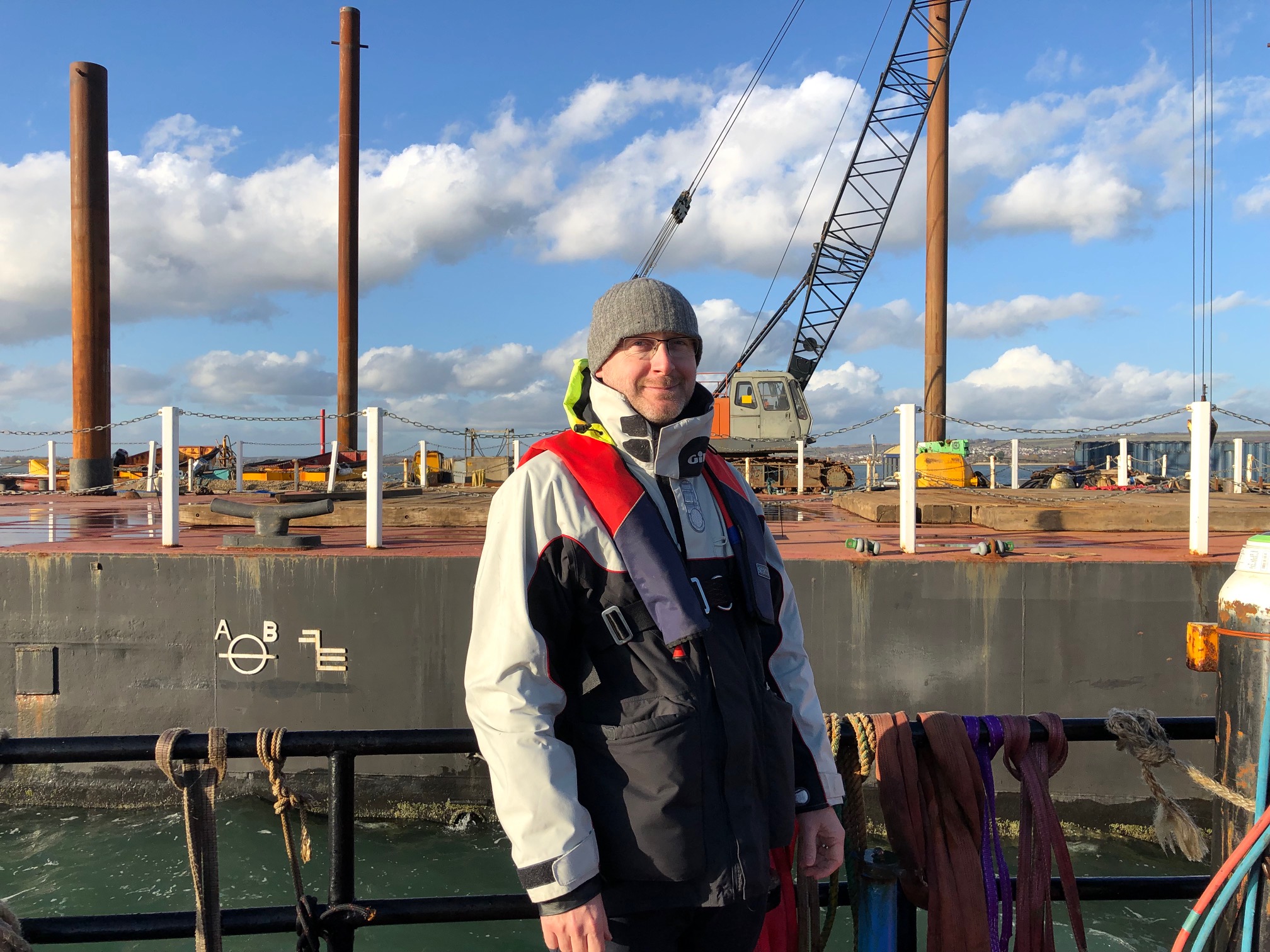
Baker Trayte Marine Ltd, established in 1993, is a company located in Portsmouth, Hampshire that conducts a variety of marine work. They hold a high reputation for their standard of service and workmanship, which has resulted in them being awarded a number of valuable contracts from a range of credible authorities such as the Ministry of Defence. As a result of these high standards, they felt it was an important step for their business to obtain ISO 9001 accreditation, which we helped them to achieve.
Recently, Baker Trayte Marine had a surveillance audit to ensure that the quality management system (QMS) that we had assisted with putting into place was still being practised with full effect, including all measures and procedures that had been implemented. We are very pleased and proud to announce that, with our on-going help, Baker Trayte had passed their surveillance audit without a single non-conformance raised – evidence that the business is working hard and dedicated to their QMS.
Baker Trayte is the latest success when it comes to ISO 9001 audits, and we hope that our working relationship continues to be fruitful.
If you require any assistance with a quality management system or with achieving ISO 9001 certification, please do not hesitate to contact NPT Management Systems today.
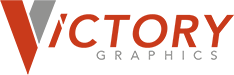
Victory Graphics are a company whom we previously helped to achieve ISO 9001 certification. As plans for future growth included a position as Quality Driver, incorporating a fully-functional QMS (Quality Management System) seemed a logical choice for the company moving forward.
Some time after Victory Graphics were initially awarded ISO 9001 certification, a surveillance audit was needed to ensure that the QMS was working effectively and that the procedures that we helped them to put in place were current and up to date. We are glad to report that, with our help, Victory Graphics passed the surveillance audit without a single non-conformance raised - a testament to the business's hard work and dedication to quality.
This is the latest success in our working relationship with Victory Graphics, hopefully with many more to come in the future!
If you require any assistance with a quality management system or with achieving ISO 9001 certification, please do not hesitate to contact NPT Management Systems today.
A number of businesses within various industries use ISO certification as a recognised method of producing and delivering control of quality products and services and customer service. ISO accreditation not only provides improvements and quality to processes and methods but is often recognised as a mark of uniformity of both products and services across countries, languages and cultures. Therefore, by a business obtaining ISO certification, it is seen as a huge positive in terms of reputation and image, as well as in terms of practicality. Some businesses, however, may benefit more than others from the implementation of ISO practices, such as manufacturing companies.
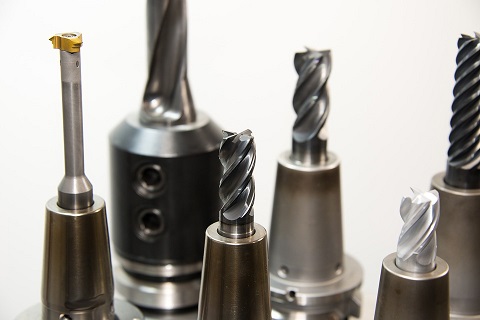
How ISO Certification Helps Manufacturing Companies
Specific clauses within ISO certifications, such as ISO 9001, outline guidelines and processes on the way a business should carry out certain practices. These help manufacturing companies to improve crucial areas of their business, such as;
- Standard of Product - As mentioned, ISO certification addresses the issue of product quality. By implementing specific processes, product definition can be accurately prescribed to ensure that each product is consistently manufactured to a consistent level of standard.
- Corrective Action Processes – Section 10.2 of ISO 9001 concerns itself with ‘nonconformity and corrective action.’ To prevent nonconformity is of utmost importance, but if an incident was ever to occur then displaying corrective measures and ensuring that it doesn’t get repeated is vital to any quality management system, as well as an exceptional way to develop trust between business and customer.
- Quality Tollgates – An integral part of many sections of ISO 9001, there are many instances where the application of evaluation and measurement is necessary to create a ‘tollgate’ on product quality. The enables manufacturing companies to gain data and knowledge to be able to drive continuous improvement needed by all organisations.
- Knowledgeable and Motivated Employees – With the implementation of ISO practices, issues such as ‘awareness’, ‘competence’ and ‘organisational knowledge’ are covered which enable members of staff within a manufacturing company to perform to a high standard in producing products and services. As well as being highly competent, with ISO certification, manufacturing businesses will put into place strict and clear training processes, roles and the ability to show accountability of management. All of which will lead to a more satisfied and motivated workforce.
These are just a few of many elements that enable manufacturing companies to perform more effectively with ISO certification. If you require advice on ISO accreditation, please do not hesitate to contact NPT Management Systems today.
Get in Touch >